Midas
Technology
|
|
|
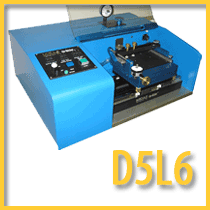 |
D5L
Series De-Lidder
D5L6, D5L8, and D5L10 de-liddersTM are designed for
straight-sided packages such as bathtub, DIP and butterfly hybrids and
multichip modules (MCMs). They share all the Generation-5 improvements,
differing only in their size and maximum package capacity. Parts are
normally positioned lid-down on the work surface, held in place by
torque-limited screws. They align against a datum stop (gold coloured
fixture shown to the right). The datum stop is adjustable, exposing a
precisely controlled width of lid flange to the cutting tool. The tool
spindle is adjustable vertically, to remove the precise height of the lid
flange without cutting into the package wall – so you can reseal without
sanding. The package cavity is kept completely free of particles by
hold-down pressure on the package wall, tool geometry, and high-velocity
vacuum applied around the cutting tool by the D5VAPS particle control
option. The easily-changed standard fixture has a low shelf for up to ½"
side leads and a through-slot for lead frames. The entire machine is quickly
adaptable to special applications including lid-up operations for
solder-sealed parts and formed lids. All D5L machines accept the D5RT
Turntable Module for removing caps from TO headers & round parts.
DL5 Series Brochure (PDF) |
|
D5F Series
De-Lidder
D5F6 and D5F8 de-liddersTM are designed for
straight-sided packages with attached optical fibres. As with our D5L
models, parts are normally positioned lid-down on the work surface, held in
place by torque-limited screws. However D5Fs have vital fibre-friendly
features developed in collaboration with top optical manufacturers. The D5F
hold-down system slides open so fibres can be positioned without catching on
rods or screws. The table is spaced farther from the tool spindle so excess
bending or tight coiling of fibre bundles is not required. When parts are
aligned against the datum stop (silver-coloured fixture shown to the right)
fibres rest on protective trays. These features make D5F machines physically
larger and costlier than their D5L counterparts, but they have proven highly
successful in operation. The datum stop is adjustable, exposing a precisely
controlled width of lid flange to the cutting tool. The tool spindle is
adjustable vertically, to remove just the lid flange without cutting into
the package wall – so you can reseal without sanding. The package cavity is
kept completely free of particles by hold-down pressure on the package wall,
tool geometry, and high-velocity vacuum applied around the cutting tool by
the D5VAPS particle control option. |
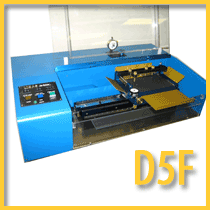 |
|
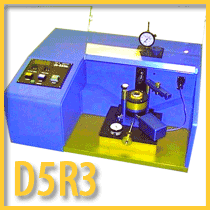
|
D5R3
De-Lidder
The
D5R3 (rotary) de-lidderTM brings our proven
rectangular lid removal technology to facilities that work only with round
packages and headers. Our kovar-optimized micrograin carbide tools mill
through the cap flange and weld interface as the part rotates on a motorized
precision turntable, recreating a smooth reseal surface on the original
header. Width of cut is adjusted by moving the turntable toward or away from
the cutter. Cut depth is adjusted by raising or lowering the tool spindle.
Platter fixtures for each package type provide accurate centring. Built-in
tool cowl and conductive hoses pull debris away from part into (optional)
59db cleanroom vacuum. |
|
D5RT
De-Lidder
The
D5RT Module replaces the worktable on the D5L6
de-liddersTM with a motor-driven precision turntable, giving
operators a convenient de-lid process for round packages and headers. A
leadscrew moves the table toward the cutter (referenced by a dial
indicator), so width and depth can be adjusted while the cutter is turning.
Once plugged in, the D5RT operates via the host machine’s control panel.
Package-specific platter fixtures provide the accurate centring that is
critical for round designs |
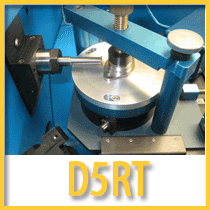 |
|
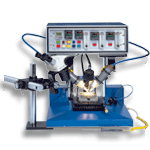 |
HGRS-V
Hot Gas Rework Station
The HGRS-V succeeds where solder-reflow units fail.
Its' unmatched thermal capacity (just enhanced with faster and longer-life
heating elements), precision heat footprint and sophisticated shear/
workholder system minimize cycle time, avoiding excess heat transfer.
Adjacent devices are protected with cooling jets and a max temperature limit
settable anywhere on your circuit. This version has our 6"x6" travel
workholder, with options for up to 12"x12" parts, plus fast sampling
controllers, a more comfortable shear drive system, fibre optics, and
leadscrew X- and Y- positioning with an integrated vacuum system for die
placement and reflow.
HGRS-V Brochure (PDF) |